けたろーです。 年々、月日の移ろいを早く感じてます。 歳がいくとホント早いっす。。 (^_^;)
さて。
トーマス・エジソンは、
人生における失敗者の多くは、
トーマス・エジソン
諦めた時にどれだけ成功に近づいていたかに
気づかなかった人たちである。
という言葉を残しています。
ボク自身、何をもって、失敗というのか? はたまた、何を持って、成功というのか、未だによくわかっていないんですけどね。 ものづくりを生業にしていて、自分で設計をしているので、ものづくりには失敗がつきものなんじゃないかな… なんて思ったりします。
一方で、自分が目論んだ通り、一発で全てがうまくようなときは格別な想いもあります。 でも、逆に、一発でうまくいくと、その本質が見えにくくなることも大いにあります。 うまくいってるから、特に問題はない… ということで、それ以上の考察や発展には至りにくいのです。 (めんどくさくなるというのがホンネですが… w)
しかし、うまくいかなかった場合には、『なんでなんや?』と考察や探求が始まり、うまくいかせるために知恵を働かせて、更なる工夫や改良をしていくわけです。 ということを思うと、失敗から得る経験や体験、知恵の方が大きいのかなと思ったりもします。
結局のところ捉え方の問題で、〝失敗〟って言ってしまえばただの失敗で、それを次のステップだと思えば新しい経験や知恵を得たことになりますよね。 まぁ、後から思えば的な面が大きいのだけど。
前振りが長くなったのだけど、今日の話題は、過去の失敗談から。 納めて、うまく行ってたはずが… というやつです。
全体を把握することの重要性。
少し前のブログで、粒状製品の計数・充填装置を作ったことをお伝えしました。
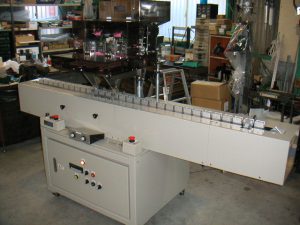
これには、後日談があるんです。
客先へリリースしてからしばらくは、うまく使って頂けているようでした。 なので、うまくできたと安心していたのです。 しかし、その状況も長くは続きませんでした…
計数ミスが発覚。
ある日のこと。 計数でミスが起きた! と連絡が入りました。
規定数入っているはずが、入っていないとのクレームがでたとのことでした。 数えるヒマ人もいるんですね…
この時の計数方法は、一種の〝枡計量〟方式を採用していて、穴に入れてカウントするのでミスは起こりようがないと絶対的な自信を持っていただけに、クレームは信じがたいものでした。 しかし、調べていくうちに重大なことがわかったのです。
計数を行う製品は、粒の表面を糖成分でコーティングしている『糖衣された』粒状の製品でした。
設計を行う際にサンプルとして頂いていた製品は、形状、サイズ的に少し不揃いな感じはあるものの、極端な差はなく、計数するにはそれほど問題ではないという印象でした。 それを踏まえて、計数方法を吟味し、機械を設計したのです。
機械が完成した時点で、試運転用のサンプルを頂き、動作チェックを十分行った上で客先へ納品。 むろん、現地でも十分な検証を行って現場へリリースを行ったつもりだったのですが…
原因は、異物。
計数として採用した方法を詳しく言うと、粒が一粒入るサイズの穴を計数分だけ開けた専用のプレートを使って、その穴に粒を入れ込み、次いで、容器への充填時にセンサーを併用して数を数えるような仕組みを用いていました。
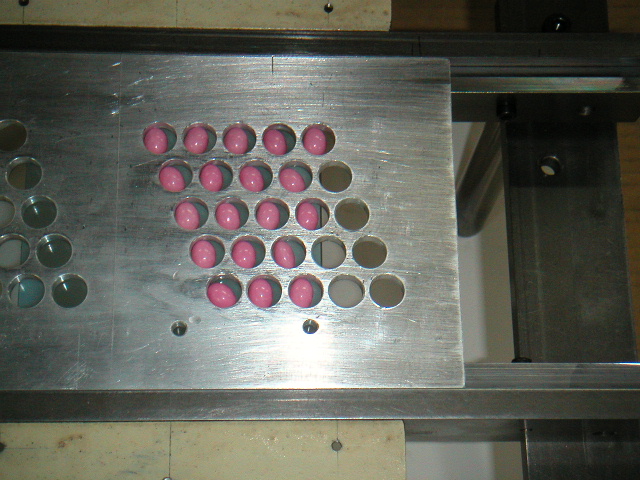
容器に注ぎいれるための漏斗状の受け口に粒を落下させるタイミングでセンサーでそれをキャッチし、数を数え、専用の容器に入れるといった流れで構成したのです。
穴のサイズは粒が1個しか入らない大きさなので、この方式を用いれば確実に計数ができて、ミスはあり得ないと思っていたのです。 …が、調べた結果、製品の粒自体には問題はなくて、原料として供給される製品の中に『糖衣の欠片や塊=カス』が混じっていて、それが計数ミスの引き金になっていたことがわかりました。
作業場に入荷された原料としての製品は、欠片などの選別を行うこともなく、そのまま、本機のホッパー(※)へ投入されます。 (※ 原料をためるところ。) 計数用の穴に製品が入る際に、その〝カス〟が穴に入ってしまって、センサーがそれを検出し、計数してしまうというのがミスの原因でした。
糖衣の破片や糖衣の塊が混じることなんて全く想定もしておらず、元はと言えば、そういった部分が原料のなかに混入することがそもそもまずいんじゃないのか? 一種の異物混入なのではないのか? と思い、と先方に伝えたところ、糖衣の製法上、混入は致し方ないと一蹴されてしまったのです。(A;´・ω・)アセアセ
今後の再発防止策として、カスや塊などの異物を除去し、選別してから入荷してもらうか、もしくは、原料を投入する際に選別するようにすればいいのでは? と伝えたのですが、ユーザーからはコストがかかるのでできない・・ と言われました。
最終的な結末。
機械を改造して、カスなどを除去するような対策をすれば何とかなりそうだったのですが、そういった〝不良物〟を100%除去することは約束しがたく、また、できたとしても予算がないとのことでしたので、結局は、うちとしてもどうすることもできないという結論に至ったのでした。
つまり、残念ながら、機械はお蔵入り。(あ、相手側の事由でしたので、機械代は頂けましたが・・)
今回の機械を導入されるまでは、数名のスタッフを配置し、似たような方式を用いて人海で作業をされていたようです。 人手で行うため、当然、カスや異物は都度除去できます。 そう考えると、こういう状況は〝確認できていたこと〟であって、彼らからすれば、ほぼ認知されていたことというわけです。
機械をつくるというのは、
現状の課題を〝機械という形〟に置き換えて、克服する。
ということでもあります。 なので、どんな些細なことであれ、事前に分かっていることや、現状の課題や状態を相手にありのまま伝え、共有するということがポイントです。
概ね、開発を依頼される場合で渡されるサンプル品は、きれいなものが多すぎるキライがあります。 きちんと整ったものがサンプル品として手渡される。 これは、ある意味において正解なのですが、ある意味において厄介なのです。
サンプルで手渡される状態のモノが、実生産の場合とまったく同じなら問題はありません。 ですが、稀に、お預かりしたサンプル品と、実生産時とで異なっている場合があります。 例えば、表面の質感(肌触り、表面のツヤなど)、サイズ、形状などが異なる場合がそれです。 また、包装資材などに多いのですが、包装資材側のソリや大きさの不均一、材質違いなどといったことも同じです。
今回の件でいうと、頂いたサンプルの中には、カスや塊といった異物はありませんでした。 結果論になりますが、事前に〝欠片や塊が混入します〟というアナウンスがあれば何かしらの対策を考えれたのかもしれません。
このケース、後味がすごく悪かったです。 こちらとしても、もっと想像力をわかせて、設計に臨まねばという教訓にもなりました。
ご相談、お問合せはお気軽にどうぞ。